[FKFU-A259-00-A] Frontloading CFD - Required Technologies
작성자
플로우마스터코리아
작성일
2021-11-04 16:15
조회
1247
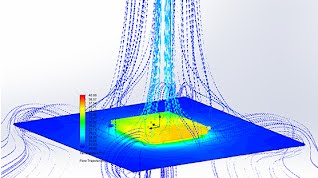
quality products in a shorter time. With engineering simulation technology, increasing product complexity can be designed much closer to its limits and therefore overdesign can be reduced - but it has a knock-on effect of more and more requests for Computer-Aided Engineering (CAE) simulations by stretched simulation experts.
Frontloading of all sorts of simulations, including Computational Fluid Dynamics (CFD), into the design department is the “gold standard” with the highest ROI, and it is playing an increasing role while being accepted widely, especially in the automotive industry.
Such frontloaded CFD simulations need to be done directly on the latest 3D Computer Aided Design (CAD) model and need to provide results in hours rather than days or weeks. The inherent higher order numerical nature of CFD simulation tools can make them very complicated and demand a deep understanding of both the physics and numerical algorithms involved. The utilization of well-known CFD methodologies such as the Finite Volume Method (FVM) for solving the underlying Navier-Stokes equations are generally required but facilitating technology enablers are actually the synergies between numerical, engineering techniques and analytical methods. These provide the foundation to reducing the numerical skill requirements and the manual time spent on such tools for meshing a given geometry, not only for engineers but also for analysts.
Efficient use of CFD tools embedded into CAD systems requires the development of special approaches. These approaches should allow for the solving of tasks based on complex CAD geometry. By applying analytical methods to numerical tasks, physics describing the behaviour of a fluid boundary layer for example can be used to reduce
the required skills for building high accuracy meshes and the manual time spent on the geometry and grid generation task by an order of magnitude. A relatively coarse CFD mesh can be applied via this approach and the sub-mesh physics can be overcome with the implementation of analytical data. As a result, the considered approach enables a reduced cell count compared to meshes with thin boundary layers being meshed. This approach also enables the use of an automated Cartesian mesh with Cartesian-based polyhedral cells at the fluidsolid interface as well as solid-solid interface, thus eliminating the laborious manual work of creating a fine boundary layer mesh. Instead, it enables the automation of the meshing process completely with very low numerical skills or time requirements for the engineer or the analyst.
The SmartCells™ based frontloading CFD approach will be elaborated in this paper. It has proven successful in a wide range of applications and is applied by OEMs and Tier 1 suppliers in the automotive, aerospace and other industries. Several benchmark examples will be presented to illustrate the approach. The methodology described here ultimately enables the use of CFD in the design process by CAD engineers and automates tedious CFD meshing by an order of magnitude within common CAD environments and PLM workflows without compromising the resulting accuracy compared to typical traditional CFD solutions even with coarse meshes.